Developing interaction & stimulating innovation to benefit Northern Ireland
Connected is here to encourage, ease and increase potential knowledge exchange links between academia and industry, particularly small and medium-sized enterprises (SMEs).
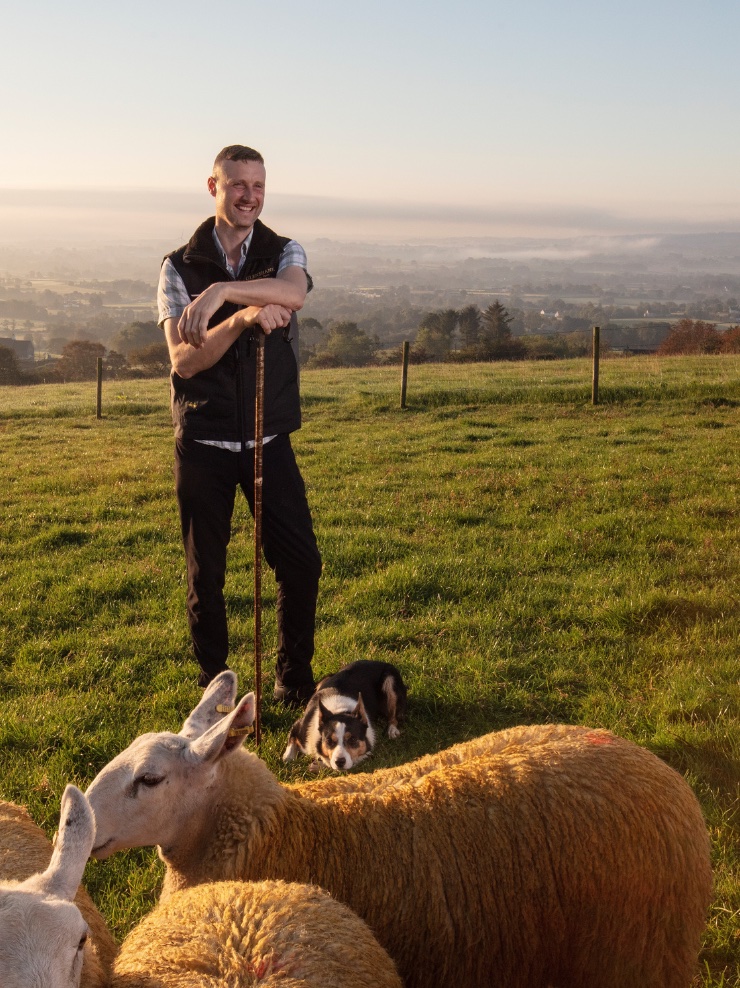
NWRC and Glenshane Country Farm
Read Case Study
SERC QUB & EcoDepo
Read Case Study
NWRC AND An Margadh Ltd
Read Case StudyAbout Connected NI
- Funded by the Department for the Economy, Connected was the first Knowledge Exchange programme in the UK to be delivered across both Higher and Further Education.
- Through Connected, we can open up a world of expertise and world class facilities to local business.
- We give companies of all sizes access to the full range of services available from local universities and colleges.
Project Partners
An accumulation of decades of experience
Covering a broad range of expertise
Project PartnersNews & Events
Check out our latest Connected NI news stories
Click for upcoming news and event stories
News & Events